- Home
- >
- Products
- >
- Electrical Parts Mold
- >
- Tension Meter Plastic Housing Injection Mould
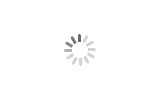
Tension Meter Plastic Housing Injection Mould
Brand :Focare
Product origin :China
Delivery time :60 days
Supply capacity :500 molds per year
Since the annual output of tension meter is not large and the customer needed to save cost, they decided to put all the plastic parts of the tension meter on the same mold. Due to the high requirements of the appearance quality of the plastic parts and the high requirements of the size and assembly accuracy, the mold we designed adopts the multi cavity and multi parting surface.
Tension meter is mainly used in printing, packaging, plastic, paper, cable, non-woven and other industries related to coil processing. The main functions of tension meter are to control the tension of the material belt when it is transported on the equipment for a long time, and ensure that the material belt is not damaged. Generally, it is used together with the transmission equipment such as magnetic powder clutch and magnetic powder brake.
Since the annual output of tension meter is not large and the customer needed to save cost, they decided to put all the plastic parts of the tension meter on the same mold. Due to the high requirements of the appearance quality of the plastic parts and the high requirements of the size and assembly accuracy, the mold we designed adopts the multi cavity and multi parting surface.
How to determine the parting surface of the plastic housing, the factors which need to be considered are more complex. As the parting surface is affected by many factors such as the molding position of the plastic part in the mold, the design of the injection system, the structural technology and accuracy of the plastic part, the position and shape of the insert, the pushing out method, the manufacturing of the mold purpose, the venting and the operation technology, etc., it is necessary to make a comprehensive analysis and comparison when choosing the parting surface so as to select a more reasonable scheme from several schemes.
Generally, the following principles should be followed when selecting parting surface:
1. The parting surface shall be selected at the maximum contour of the plastic part.
2. In order to smoothly eject the plastic part, try to leave the plastic part on the moving side when opening the mold.
3. Ensure the accuracy requirements of plastic parts.
4. Meet the appearance quality requirements of plastic parts.
5. Convenient for mold processing and manufacturing.
6. The influence on forming area.
7. Impact on venting effect.
8. Influence on lateral core pulling.
In order to facilitate the mold processing and manufacturing, it is necessary to select the straight parting surface which is easy to process.