- Home
- >
- Products
- >
- Plastic Chair & Table Mold
- >
- Light Knit Plastic Dining Chair with Gas Assisted Injection
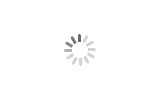
Light Knit Plastic Dining Chair with Gas Assisted Injection
Brand :Focare
Product origin :China
Delivery time :60 days
Supply capacity :500 molds per year
The advantages of gas-assisted injection molds:
1. Save raw materials, increase plastic utilization rate by up to 50%, reduce molding cycle, and improve certain performance.
2. It can reduce the pressure of the mold by 60%, make the size of the part uniform, and improve the shrinkage and deformation.
3. Reduce the working pressure of the injection system and the clamping system of the injection machine, so that the mold is suitable for smaller machines and reduce power consumption.
4. The requirements for the injection molding machine system are relatively simple, and there are no special requirements for raw materials.
The advantages of gas-assisted injection molds are as below:
1. Save raw materials, increase plastic utilization rate by up to 50%, reduce molding cycle, and improve certain performance.
2. It can reduce the pressure of the mold by 60%, make the size of the part uniform, and improve the shrinkage and deformation.
3. Reduce the working pressure of the injection system and the clamping system of the injection machine, so that the mold is suitable for smaller machines and reduce power consumption.
4. The requirements for the injection molding machine system are relatively simple, and there are no special requirements for raw materials.
However, there are also disadvantages. The requirements for the mold are high. In the early stage, the feasibility of the intake air must be repeatedly demonstrated. The later production is more complicated than the ordinary injection molding. The adjustment personnel must pay attention to collecting relevant data. In production, it is adjusted repeatedly. Master the characteristics of inert gases.
1. Gas-assisted process characteristics
(1). The influence of gas penetration on the process parameters should be considered. The primary penetration of gas-assisted molding depends mainly on the proportion of plastic melt volume in the cavity and is governed by the laws of fluid mechanics. Secondary penetration occurs at thicker locations and expands in all directions. The influence of process parameters on the strength of gas penetration is mainly reflected in the gas penetration length and the plastic thickness of the airway surface layer. In general, higher gas injection pressures, higher melt temperatures, lower melt viscosity and shorter switching delay times result in shorter penetration lengths and thinner airway wall thicknesses.
(2). It is recommended to use low-pressure gas when filling the mold. When the pressure is maintained, the pressure is compensated for shrinkage. The reason is that some gas will be dissolved in the boundary layer where the melt is in contact with the gas. If the plastic is not fully solidified after the pressure is maintained, the pressure is reduced. These gases will swell to cause air bubbles on the inner surface of the airway. The greater the gas pressure during filling, the more gas is dissolved in the boundary layer of the melt, and the stronger the gas expansion effect after the pressure is maintained.
(3). Care should be taken to avoid excessive turbulence and cause extensive gas expansion on the inner surface of the airway.
(4). Efforts must be made to avoid the injection, because the melt will overlap and free surface cooling in the case of jetting, and the gas will blow through the melt surface when it penetrates into the first overlap in such a non-uniform melt. Causes molding failure. It is possible to fill the cavity in the direction of the reverse gravity and start filling at the thinnest part of the product to avoid spraying.
(5). In the switching time when the gas injection has not started before the end of the melt injection, try to avoid a large change in the melt flow rate, because this change will cause hysteresis line and gloss change on the surface of the product.
(6). Quantity and material accuracy: The core of the actual gas-assisted process is the amount of material, the amount of material and the accuracy of the injection molding machine, which will affect the effect and stability of the gas-assisted process. The reason is: when the mold cavity is filled with plastic, it is difficult for the gas to form a cavity inside the plastic. Only in the state of lack of material, the position of the air cavity is left. When the gas is injected into the cavity, the preset plastic is The entire cavity is filled by the expansion of the internal gas. Therefore, the amount of material is directly related to the molding effect of the gas-assisted process, and the error of the accuracy of the plastic machine is related to the stability of the gas-assisted process. Gas-assisted injection molding does not necessarily ensure that all plastic is injected into the cavity.
2. Gas assisted process adjustment method
When the gas-assisted process is adjusted, it is recommended to adjust accordingly in the following order:
(1) In the case of no gas injection, first fill the product and observe the flow state of the plastic and the state of the mold;
(2) Gradually reduce the amount of material, observe the distribution average of each gate flow when the material is missing, and try to ensure the flow symmetry of the mold;
(3) The general gas-assisted process generally uses two-stage or three-stage gas injection. The thin-wall part pressure is suitable for high-pressure gas injection 2500--4000 psi, and the thick-wall or rod-shaped product is suitable for low pressure gas injection 1000--2500 psi.
(4) When the material shortage reaches about 90%, gas injection starts. If there is still some shrinkage in the product, it is recommended to reduce the material amount appropriately until the product is not full, and then add the material amount to the full state.
(5) Adjust the gas pressure appropriately, and the gas holding time and starting delay are in a suitable state.
(6) In the nozzle intake mode, be sure to use the reverse seat to exhaust.
(7) In the air intake mode, it is important to pay attention to whether the air needle exhaust is unobstructed. If the exhaust is not smooth, it needs to be cleaned in time.
3. The gas-assisted injection molding process can be divided into four phases:
The first stage of gas-assisted injection molding: plastic injection. The melt enters the cavity and encounters a lower temperature mold wall to form a thinner solidified layer.
Gas-assisted injection molding second stage: gas incident. The inert gas enters the molten plastic, pushing the unsolidified plastic into the cavity that is not yet filled.
The third stage of gas-assisted injection molding: the end of gas injection. The gas continues to push the plastic melt flow until the melt fills the entire cavity.
The fourth stage of gas-assisted injection molding: gas holding pressure. Under pressure, the gas in the air passage compresses the melt and feeds to ensure the appearance of the part.