- Home
- >
- Products
- >
- Industrial Parts Mold
- >
- Two-Component Screwdriver Handle Plastic Injection Mould
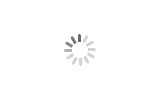
Two-Component Screwdriver Handle Plastic Injection Mould
Brand :Focare
Product origin :China
Delivery time :90 days
Supply capacity :300 molds per year
Product Material:PP+TPE
Mold Cavity:3+3 cavity
Mold Main Material:H13 with hardness 45-48HRC
Mold Injection System: 6tips hot runner system
Mold Size:550X510X400 mm
Suitable Machine: 280ton two component injection mold machine
A screw driver is a tool for screwing and unscrewing screws.
The typical simple screwdriver has a handle and a steel shaft.
Handles are typically wood, metal or plastic.
The two-color handles of screwdriver generally are made by two steps injection procedure.
The steel shaft put into molds first, then make the 1st injection of rigid plastic PP.
The second injection could be made by horizontal or vertical injection.
If made by horizontal injection, it is suggestion to use rotary axis double color injection machine which have two injection units.
After making the 1st injection of rigid plastic PP, the core of mold will rotate to the other side, then make the 2nd injection of TPE soft material upon PP.
If made by vertical injection of second component, the mould will have two punches and one cavity.
During making injection of the first punch, the operator will put the screwdriver handles on the second punch.
No matter which process will be used, two-color injection molding refers to the injection molding of two different materials into the same set of molds, so that the injection molded parts are formed by two materials or two-components.
Some of the two materials are different colors, and some are soft and hard, which improves the product's aesthetics and assembly performance.
Advantage editing
Compared with the traditional injection molding, the two-color molding process has the following advantages:
1. The rigid plastic material can use low viscosity materials to reduce the injection pressure.
2. From the perspective of environmental protection, the inner material can use recycled secondary materials.
3. According to different use characteristics, such as thick pieces of finished leather layer using soft materials, inner materials using rigid materials can use foam plastic to reduce weight.
4. Lower quality inner materials can be utilized to reduce costs.
5. The cortical material or core material can be used expensive and special surface properties, such as anti-electromagnetic interference, high electrical conductivity and other materials to increase product performance.
6. The proper cortex material and core material can reduce the residual stress of the molded product, increase the mechanical strength or the surface properties of the product.
7. Produce products such as marbled roads.